SGめっきとは
SGめっきは、弊社で行っている「溶融亜鉛アルミニウム合金めっき」の名称で、5%のアルミニウムだけでなく、1%のマグネシウムも添加した合金めっきです。亜鉛にアルミニウムを添加すると耐食性が向上することは以前より知られており、連続めっき鋼板の分野では1970 年頃にすでに商品化されていましたが、一般的な溶融亜鉛めっきの分野ではそこまで注目されていませんでした。そのような状況の中、弊社では亜鉛アルミニウム合金めっきの技術にいち早く注目し、1980年頃から実用化に向けた開発を始め、独自の技術も加え、このめっきを可能としました。
この技術の特長は、亜鉛にアルミニウムだけでなく、マグネシウムも添加することにより、さらなる耐食性の向上を狙ったところにあります。
このめっきは、ベースとなる溶融亜鉛めっきと同様に、鉄表面にめっき皮膜を作り、空気や水分との接触を防ぐことによって、さびから”鉄”を守る技術です。さらに、添加された、アルミニウム、マグネシウムにより、従来の亜鉛めっきでは得られない高い防食効果を得ることができます。
SGめっきの特長
1. 高い耐食性
溶融亜鉛めっきと同様、「保護皮膜作用」と「犠牲防食作用」という2つの働きがあります。
・アルミニウム、マグネシウムの効果
SGめっきは、溶融亜鉛めっきと同様に、時間の経過とともに腐食生成物を生成します。この腐食生成物がめっき皮膜を保護し、腐食から鋼材を守っています。
しかし、亜鉛めっきでは、海塩粒子などの腐食因子が多く飛来する強腐食環境では、腐食生成物の保護作用の効果はあまり高くなく、時間の経過とともにめっき皮膜の亜鉛は徐々に消失し、鉄を守るという働きは次第に失われていきます。
それに対して、SGめっきでは生成した腐食生成物に、めっき皮膜中のアルミニウムやマグネシウムが作用し、強腐食環境においても腐食生成物が安定して存在し、保護皮膜として働きます。その結果、皮膜の消費が抑えられ、腐食が抑制されていきます。
2. 経済性に優れる
SGめっきは、亜鉛めっきと比較して長期間の耐食性が期待できるため、メンテナンスフリーとなり、ライフサイクルコストの点から、経済的に長期防錆を維持することができます。
3. 塗装下地として優れる
化成処理性がよく、塗装との強固な密着性が長期に渡って確保できます。したがって、塗膜に傷が付いても、そこからの劣化はほとんどありません。また、焼付塗装の際、塗膜の発泡現象(ブリスターの発生)がほとんど無く、塗装不良も激減できます。
4. 環境に優しい
RoHS指令などに記載される環境負荷物質(鉛やカドミウムなど)をほとんど含まない、環境対応型のめっきです。
めっき工程
SGめっきの工程は下記の通りです。
めっき規格
SGめっきに関する規格には、日本産業規格:JIS H 8643(溶融亜鉛アルミニウム合金めっき)があります。
下記に、抜粋したものを示します。
①種類及び種類の記号(項目:4)
表 種類及び種類の記号
種類 | 種類の記号 | 適用例(参考) | |
---|---|---|---|
1種 | 25A | HZA 25A | 直径12mm以上のボルト、ナット、厚さ2.3mmを超える座金など。 |
36A | HZA 36A | 厚さ1.6mm以上の鋼材・鋼製品など。 | |
50A | HZA 50A | 厚さ6.0mm以上の鋼材・鋼製品、鋳鍛造品など。 | |
2種 | 18B | HZA 18B | 直径12mm以上のボルト、ナット、厚さ2.3mmを超える座金など。 |
25B | HZA 25B | 厚さ1.6mm以上の鋼材・鋼製品など。 | |
35B | HZA 35B | 厚さ6.0mm以上の鋼材・鋼製品、鋳鍛造品など。 |
注
・種類の1種は、磁力式試験方法によって試験ができるものに適用する。
種類の2種は、磁力式試験方法によって試験ができないため、JIS H 0401 5.2(間接法)によって試験を行うものに適用する。
・亜鉛めっきのように「比重」を用いて、膜厚から付着量、付着量から膜厚への換算は行いません。
②膜厚および、付着量(項目:7.3、7.4)
種類が1種のめっきの膜厚は下表による。
表 1種の種類の記号及び膜厚
単位 μm
記号 | 平均膜厚 | 最小膜厚 |
---|---|---|
HZA 25A | 25以上 | 18以上 |
HZA 36A | 36以上 | 25以上 |
HZA 50A | 50以上 | 36以上 |
種類が2種のめっきの付着量は下表による。
表 2種の種類の記号及び付着量
単位 g/m2
記号 | 付着量 |
---|---|
HZA 18B | 180以上 |
HZA 25B | 250以上 |
HZA 35B | 350以上 |
※ JIS H 8643:2019(溶融亜鉛アルミニウム合金めっき)より抜粋(掲載許可済)
めっき組織
SGめっきの皮膜は1浴目の溶融亜鉛めっき皮膜中の鉄-亜鉛合金層がベースとなって形成されます。以下に1浴と2浴の金属顕微鏡によるめっき組織および、EPMAによるめっき皮膜中の各成分の分布を示します。
1浴目の組織は溶融亜鉛めっきと同様で、鉄素地に接して鉄-亜鉛の合金層があり、さらに上層(皮膜表面側)は純亜鉛層となります。SGめっきの組織は、アルミニウムやマグネシウムが1浴目で形成された鉄-亜鉛合金層中に拡散・浸透して合金化し、さらに上層に浴成分層が形成されます。めっき工法は2浴法ですが、めっき組織は溶融亜鉛めっき同様、2層構造(合金層+浴成分層)となります。
さらに、SGめっき皮膜中のアルミニウムは、めっき表面は浴成分と同様ですが、鉄素地に近づくほど濃度が高くなる分布となっていています。このアルミニウムの特徴的な分布は、時間の経過とともに腐食生成物の安定化をさらに進めることとなり、高耐食を示す重要なポイントとなります。
注:浴成分層には亜鉛の他にアルミニウム、マグネシウムが含まれています。そのため「めっき浴組成」、「冷却方法」、「断面観察時のエッチングの状況」によって見え方が違う場合があります。
耐食性
①塩水噴霧試験
SGめっき(HZA50A)および、溶融亜鉛めっき(HDZT77)の塩水噴霧試験結果を示します。溶融亜鉛めっきが1,000時間で赤錆が発生しているのに対して、SGめっきは10,000時間経過後も赤錆の発生が見られず、10倍以上の耐食性が認められています。
この結果から、生成した腐食生成物が有益に働いていることがわかります。さらに、初期の段階では溶融亜鉛めっきと比較して白錆の発生も少なく、めっき皮膜表層に存在するアルミニウムや、マグネシウムの酸化皮膜がバリヤーとなって腐食環境から保護していることもわかります。
②大気暴露試験
耐食性の試験方法として、塩水噴霧試験のほかに実際の腐食環境で試験を行う場合があります。以下に、北陸自動車道・徳合川橋の検査路で行った、15年間の暴露試験の結果を示します。なお、耐用年数は、めっき皮膜の90%が消失するまでの期間で表し、めっきの腐食速度とめっきの付着量から次式により算出します。
耐用年数 = 亜鉛付着量(g/m2) / 腐食速度(g/m2・年)×0.9
写真 試験場所
表 腐食速度および、耐用年数
めっきの種類 | 初期付着量 (g/m2) | 腐食速度 (g/m2/年) | 耐用年数(年) |
---|---|---|---|
SG めっき |
350 | 5 | 63 |
溶融 亜鉛 めっき |
550 | 55 | 9 |
「飛来塩分環境下における溶融亜鉛-アルミ合金めっきの曝露試験15年目の結果(第72回土木学会年次学術講演会概要集)」より
試験場所は日本海に面し海塩粒子の飛来が多い腐食に厳しい環境ですが、溶融亜鉛めっきと比較して、SGめっきの高い耐食性が確認されています。このように、強腐食環境下において高い耐食性が得られることが証明されたことは、生成した保護皮膜が腐食性因子の影響を受けにくいことを示しています。さらに、素地に近づくほどアルミニウムの濃度が高くなっていることから、このアルミニウムの作用により、SGめっきは強い腐食環境でより威力を発揮するといえます。
塗膜の密着性
SGめっきは、塗装前の化成処理皮膜が安定して形成されるため、溶融亜鉛めっきと比較して下記の特長があります。
- 塗膜の密着性が良好なため、塗膜のキズや、塗装欠陥からの塗膜の劣化の広がりが少なく、長期密着性に優れる
- 焼付塗装の場合、塗膜の発泡(ブリスターの発生)がほとんど無い
SGめっき、溶融亜鉛めっきそれぞれに塗装を行なった後、塗膜にキズ(Xカット)を入れ、塩水噴霧試験を行い、試験後の状態を観察した。さらに、カット部に沿ってテープを貼り、はがした後の状態を観察した。いずれの塗膜においても、SGめっきの方がカット部からの白さびの発生や、はがれが少ない結果が得られた。
以上のことから、SGめっきの方が溶融亜鉛めっきよりも塗膜との密着性が良好なことが確認されています。
環境に優しい
【めっき浴組成】
SGめっきは、1浴、2浴ともに最純亜鉛地金を使用し、鉛やカドミウムといった環境負荷物質をほとんど含まない、環境対応型のめっきです。下表に、最純亜鉛地金の成分表(JIS H 2107より)および、2浴の浴組成の管理範囲を示します。
表 化学成分(JIS H 2107:2015 亜鉛地金より抜粋) (%)
種類 | Zn | Pb | Cd | Fe | Sn | Cu | Al |
---|---|---|---|---|---|---|---|
最純亜鉛地金 | 99.995以上 | 0.003以下 | 0.002以下 | 0.002以下 | 0.001以下 | 0.001以下 | 0.001以下 |
2浴 浴組成管理範囲(%) | ||||
---|---|---|---|---|
Al | Mg | Pb | Cd | Zn |
4〜6 | 0.8〜1.5 | 0.01以下 | 0.01以下 | 残部 |
【めっき皮膜】
めっき皮膜の分析例を以下に示します。アルミニウムはめっき浴濃度よりも多く含まれています。また、鉛やカドミウムといった環境負荷物質はほとんど含まれていないので、環境対応型のめっきといえます。
表 SGめっき皮膜分析例
化学成分(%) | |||||
---|---|---|---|---|---|
Al | Mg | Fe | Pb | Cd | Zn |
12.5 | 0.95 | 5.27 | <0.002 | <0.001 | 残部 |
SGめっきで見られる諸現象
SGめっきでは、特有の外観上の諸現象が見られます。ただし、外観上であり、耐食性能については影響を及ぼすものではありません。
・経年変化
SGめっきの表面は、亜鉛めっきのような金属光沢は見られず、白っぽい外観です。また、亜鉛めっき同様、皮膜表面の酸化皮膜により、灰色を呈してきますが、亜鉛めっきよりも黒っぽい、暗灰色となっていきます。
また、明度の変化では、下図の場合において、SGめっきで5.2程度、亜鉛めっきで6.0程度となっています。ただし、明度の変化は設置環境に左右されるので、環境によっては暗灰色への変化が早く起こる場合もあります。
写真 経年変化
・白さび
SGめっきでも亜鉛めっきと同様に”白さび”が発生します。発生原因も同様ですので、発生を防止するには、風通しの良い場所での保管や、雨や露にさらさないことが必要です(運搬時も同様)。なお、めっき表面には保護性皮膜が形成されているので、耐食性に影響はありません。
写真 白さび
・引上模様
2浴めっき完了後、亜鉛めっき同様に、浴面に浮いた酸化物を除去しながら製品を引き上げますが、アルミニウム、マグネシウムを含有しているため、浴面での酸化皮膜の形成が非常に早く、除去しきれなかった酸化皮膜が付着して模様となって見えたものです。
写真 引上模様
・ざらつき
めっき表面に細かい凹凸が見られるものです。多くは、素材の化学成分や、表面状態に起因します。また、パイプの接合部(ビード部)などでは、線状の凸部となる場合もあります。
写真 ざらつき
写真 線状の凸部(パイプ溶接部)
・斑点模様
SGめっきの2浴はアルミニウムを含む合金であるため、2浴めっき後の冷却(空冷)の際、めっき皮膜の表層部分が徐々に凝固していく過程でごく小さい範囲で偏析が起こり、斑点状の模様となって見えたものです。
写真 斑点模様
・流れ模様
パイプ状の部材の側面から下面側に見られます。2浴から引き上げた後、パイプ下面側は引き上げ後冷めやすく、(上面の)余剰の亜鉛がパイプ下面まで流れ切ってしまう前に冷やされて固化してしまうことになります。そのため、流れた部分とそうでない部分とでコントラストができ模様となって見えているものです。
写真 流れ模様
・ピンホール
製品の部位によっては、めっき皮膜(合金浴)の凝固時に偏り(ひけ)ができ、ピンホール状に見える場合があります。部材の溶接部分に見られることが多い。
写真 ピンホール
・グラインダーがけによる黒変
たまりの修正などでグラインダー処理を行なうと処理後の皮膜が想定より早く黒変する場合があります。処理表面の酸化皮膜の成長度合いによるものと思われます。
写真 グラインダーがけによる黒変
使用上の注意点
下記に注意点を記載しますのでご配慮ください。また、使用方法によっては例外があることがありますので、弊社担当にご確認ください。
- 高温で溶かした亜鉛に鋼材を浸すため、加工物の重量や大きさに制限があります。
- 熱による歪みが生じる場合があります。
- 密封した部分や空洞にはめっきができません。
- めっき後の加工(曲げや切断など)や、溶接は避けてください。
【異種金属との接触】
SGめっきとステンレスなどの異種金属を接触した場合、使用される環境においては接触部分近傍での腐食速度が速くなることがあります。特に、海塩粒子の飛来の多いところではこの傾向が強くなります。これにより、早期腐食の恐れもあるため、SGめっきと異種金属との直接接触は避けてください。やむを得ない場合は、直接接触しない処置(絶縁ワッシャーや塗装など)が必要です。
【使用環境への配慮】
通常亜鉛めっき等の使用が適さないような厳しい特殊な環境では性能が十分発揮されず、早期に赤錆が発生するケースがあります。下記のような環境での使用時はご注意ください。場合に応じて影響を回避する対応策を併用した使用を検討いただくようご配慮ください。
- 海水中、水中、水(雨水、アルカリ水等)が溜まる環境
- 腐食促進因子が混入する環境(地際、火山灰、酸性雨、産業廃棄物、排煙、アンモニアガス等ガス類、薬品類など)
製作上の留意点
SGめっきの特性を正しく理解して使用していただくために、素材や、設計、製作上での留意点がありますので、ご配慮ください。
【SGめっきに適さない素材】
下表に該当する表面状態または構造の場合、そのままめっきすると不めっき等の使用上支障がある欠陥を生じる恐れがあるため、事前に処置をする必要があります。
表 めっきに適さない素材(JIS H 8643より)
分類 | 現象 |
---|---|
表面 |
脱脂及び酸化物の除去処理において除去できない、汚れ、油脂、塗料、さび、酸化皮膜※などの付着物があるもの。 ※酸化皮膜:レーザー切断、ガス切断、高周波曲げ、熱間圧延、熱処理、鋳造などによって素材の表面に形成されたもの。 |
素材が鋳物の場合は、砂かみ及び、巣があるもの。 | |
素材に溶接部がある場合は、溶接部のピット及び溶接によるスラグがあるもの。 | |
構造 | 空気を密閉した中空体箇所の構造のもの。 |
溶融亜鉛及び溶融亜鉛アルミニウム合金が容易に流入及び流出できない構造のもの。 | |
重ね合せ面又は突合せ面がある場合は、その面の面積が200mm×200mmを超えるもの。また、密接する面の外周が完全な連続溶接となっていないもの。 |
【素材の情報】
下記の内容については、そのままめっきすると使用上支障がある欠陥を生じる恐れがあるため、事前に御相談ください。
《構造の情報》
- ねじ付き部品について
- 異種金属との組合せについて
《化学成分》
- 素材の化学成分の情報の提供について
素材に含まれるけい素の含有量は、鉄とめっき浴の亜鉛との合金反応に影響を与えます。けい素濃度が0.05%~0.12%(質量分率)の範囲及び0.24%以上の場合には、亜鉛と鉄との合金反応が活発になることが原因で、めっきの表面に激しい凹凸、段差などが生じることがあり、その場合は、膜厚が品質を満足しない恐れがあります。また、けい素の含有量が0.01%を下回る素材では、亜鉛と鉄との合金反応が十分に起こらない場合があり、その結果、膜厚が品質を満足しない場合があります。
JIS H 8643 解説より
《設計・製作》
設計・製作上の留意点については、下記リンクをご参考ください。
https://jlzda.gr.jp/zinc/hot-dip-galvanizing/design
日本鉱業協会 鉛亜鉛需要開発センター(溶融亜鉛めっきについて/設計・補修)
めっき可能サイズ
※有効寸法以上の製品については、担当者相談へご相談ください。
ミナト西工場
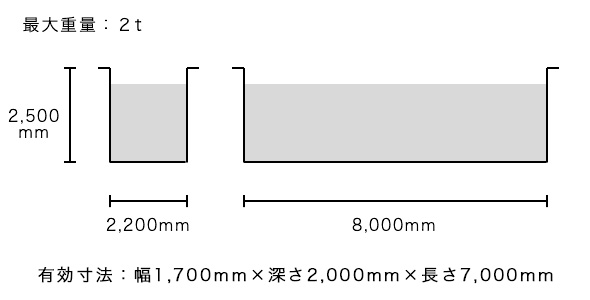
名古屋工場
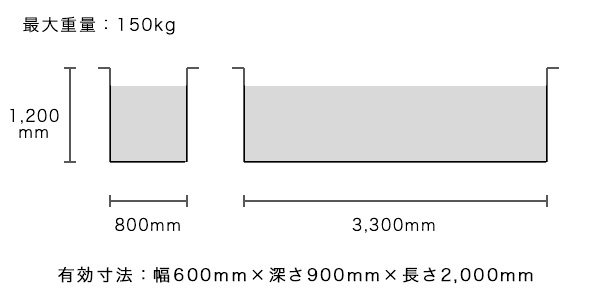